Paraffine - Ure's Dictionary, 1867
type: Beyond Scotland - Wales
From Ure's Dictionary of Arts. Manufactures and Mines, Vol III, Sixth Edition, 1867
This article from Ure's Dictionary is signed "WMW". The Birmingham Journal of 11th May 1867, in reviewing the dictionary, list many of its expert contributors, which included William Mattieu Williams. There is therefore little doubt that the article was authored by William Mattieu Williams, Chairman of Williams' Patent Mineral Charcoal and Oil Co. Ltd. and General Manager of the Pont-y-Bodkin works of the London, Leeswood and Erith Mineral Oil Co. Ltd
The manufacture of paraffine and paraffine oils from cannel and shales has now become one of the important branches of national industry The rapidity of its development is almost unexampled The few years that have elapsed between the publication of the last and the present edition of this work comprise nearly the whole period of its history during which it has extended from the single enterprise of Messrs. Young & Co to a long list of wealthy and influential companies the great majority of which have been established during the last three years and their numbers are still rapidly increasing. The most important centres are the Bathgate district which has now extended throughout nearly the whole of Linlithgow and encroaches upon Edinburghshire and the Leeswood oil district in Flintshire The Scotch oil works are almost exclusively supplied with shales of which the most important is the Boghead or Torbane Hill mineral the technical definition of which whether coal or shale was once the subject of so warm a controversy. It is found a little to the south of Bathgate It takes precedence of all the raw materials for the distillation of paraffine and paraffine oils both historically and in point of richness. It was the material originally worked by Mr. Young as above described. The other shales of the district vary considerably in richness both as regards the quantity and quality of the distilled products
In Flintshire three varieties of material are used and although they lie in juxtaposition in the same seam they are very distinct in appearance and in the quantity and quality of their products They are the curly cannel the smooth cannel and the bottom shale or "bastard cannel" .
These have been well known to exist for at least a century have been used for making blacking and as a fuel to mix with ordinary coal for giving life and flame to the cottagers fires The demonstration of their value as sources of paraffine &c is due entirely to the persevering efforts of Mr. W.C. Hussey Jones during the years of 1861 and 1862 which finally resulted in the formation of the Leeswood Green Cannel and Gas Coal Company and the oil works of Messrs. Fernie & Co at Leeswood in Flintshire and at Saltney in Cheshire. Since 1863 the extension of the branch of industry thus inaugurated has effected a change in the once quiet and picturesque valley of Leeswood, Coed Talon and the surrounding districts that can only be exceeded by the results of the gold discovery in California and Australia. The Leeswood cannel seam is from five to six feet thick in the best portions of the basin which is but of very limited area and thins out at its boundaries The upper portion of the seam consists of the smooth cannel having a thickness of about 25 to 30 inches next below is the curly cannel about 18 inches in thickness and below this the shale or bastard cannel which varies considerably both in thickness and richness It ranges from about 14 inches to 2 feet in thickness In some places especially to the westward of Leeswood this shale is replaced by a common bituminous coal which adhering firmly to the smooth cannels seriously interferes with its value as a source of burning oil the distillate from this coal containing oils of the benzole and naphthaline series giving red smoky flames. Northward beyond the river Alyn and towards Mold the whole seam thins out to 18 or 24 inches and contains only smooth cannel.
Besides these there is a bituminous ironstone similar to the black band ironstone of Scotland which comes in irregularly with the bottom shale and a black shale forming the roof above the smooth. Both of these contain oil but have not hitherto been regularly worked.
Curly cannel yields upon distillation about 30 per cent of crude oil of specific gravity varying from 875 to 890 Smooth cannel about 10 per cent of crude oil of specific gravity from 925 to 940 and the shale which is very variable yields from 12 to 15 percent of oil specific gravity about 900.
Crude oils being sold by gravity the value rising as the density diminishes the value of the curly cannel is far in excess of either of the others both on account of the quantity and quality of its yield. At the present time, 1866, it is worth from 28s to 30 per ton at the pit's mouth the prices of smooth cannel and shale being respectively about 12 and 9 per ton at the pit's month Though differing so materially both as regards quantity and specific gravity of oil produced these three minerals lie in direct contact with each other without any visible intermediate deposit nevertheless the line of separation is clear and definite and they show no tendency to run into each other Their external characteristics render them easily distinguishable They separate with moderate facility when struck with a coal hatchet and are usually worked by holeing in the smooth cannel next the roof and then wedging upwards.
Considerable modifications have been made in the mode of distillation of cannel and shales since the early operations of Messrs. Young but the amount of progress and improvement has scarcely been commensurate with the ingenuity which has been brought to bear upon the subject Some of the most promising projects have failed entirely at great cost to the projectors.
Before describing any of these projects in detail it is necessary that the nature of the process and the conditions requiring to be fulfilled should be clearly understood The cannel or shale has to be enclosed in a suitable vessel subjected to the degree of heat necessary to drive off its condensable vapours which vapours must pass through an outlet communicating with a suitable condensing apparatus
This is simple enough and for the mere production of paraffine oils from cannel or shale any kind of pot with an outlet pipe heated sufficiently by any kind of fire will suffice but to produce the maximum quantity of condensable vapours and the minimum quantity of incondensible gas with the greatest degree of rapidity and with the smallest amount of outlay in plant labour and fuel is a problem of some practical difficulty.
At first sight the distillation of crude oil from cannels and shales appears almost identical with gas making and accordingly the early retorts were simply copies of those found by experience to be most suitable for gas making.
It soon became understood however that some of the most important conditions to be observed are exactly the opposite of those upon which success in gas making depends In gas making the desideratum is to obtain the maximum amount of permanently elastic gas and the minimum of condensible vapours in oil making we require to reduce the permanent gases to the minimum or if possible to make none and to obtain in their place the greatest possible quantity of condensible vapours It is now well known that if these condensible vapours are exposed to a high temperature they are decomposed and to a considerable extent converted into permanent gas and that the proportion of permanent gas bears some relation to the excess of temperature the greater the heat the more incondensible gas and the less condensible vapours are formed In gas making therefore a very high temperature is desirable in oil making the great object is to subject the coal to no excess of temperature beyond that which is absolutely necessary for its distillation into condensible vapours.
The mischief done by excessive heat is by no means limited to the mere loss of the percentage of vapour converted into permanent gas for in addition to this the oil produced suffers a serious deterioration In the manufacture of paraffine oils the C2 H6 series of oils are required a high temperature converts these into a different series the precise nature of which has not yet been by any means satisfactorily determined It is commonly stated that the benzole and naphthaline series are thus produced from cannels and shales This however is but a loose assertion for though it may be possible to produce these at certain high temperatures no one has yet determined what those temperatures are and there is little doubt that at the intermediate temperatures an intermediate series of uninvestigated products are formed.
Without dwelling further on obscure theoretical considerations we may state generally that the practical result of excessive heat is besides a wasteful production of permanent gas the production of a crude oil of darker colour higher specific gravity and possessing a characteristic odour well known to practical oil makers as that of burnt oil This burnt crude oil contains less solid paraffine and is much more difficult to refine than crude oil made at a lower temperature from like material It requires much more acid treatment and even then produces burning oil which still retains the burnt odour and blackens the lamp glasses
The difficulties standing in the way of distillation at the proper temperature are:
- 1st, the necessity of decomposing before distillation
- 2nd, the varying boiling points of the different products
- 3rd, the law of radiation which demand a higher temperature in the retort than that of the coal and
- 4th the commercial necessity of rapid working
We will consider these seriatim and in describing the improvements and attempted improvements in retorts refer each to the difficulty that it aims to overcome
- 1 st - Although these hydrocarbons known as paraffine oils and paraffine are obtained from the cannel by distillation it is quite clear that they do not exist there as such We may saturate a mass of the porous cannel coke with these hydrocarbons or with crude solid paraffine and produce a flaming coal thereby which upon careful distillation will give back the volatile hydrocarbons but this artificially saturated coke is essentially different from the original cannel as shown by the fact that we may remove the hydrocarbon from the saturated coke by pounding it and washing with a solvent of paraffine &c while the cannel itself resists the action of all such solvents The same is the case with boghead and paraffine shales generally though they are not infrequently described as porous minerals merely saturated with bituminous matter by infiltration The distillation of cannels and shales is thus a more complex process than the distillation of a volatile oil a resin or bitumen In the latter case the substance is merely raised to its boiling point and this beat being maintained its vapour is driven off In the distillation of coal the first function of the heat is to overcome the chemical affinities which hold the hydrocarbon elements in the peculiar form in which they exist in the coal and then after this separation to drive their vapours over It is a compound process of decomposition and distillation and the heat has to overcome the combined forces of chemical and cohesive attraction Hence a considerably higher temperature than that of the mere boiling point of the resultant hydrocarbons is necessary Here then at the outset we encounter an insuperable necessity for heating the vapours considerably above their boiling points to a temperature in fact at which some degree of further decomposition must take place and some amount of permanent gas must be formed
- 2nd - The boiling points of the different volatile hydrocarbons obtainable from the cannel or shale range from about 200 to above 500 Fahr. In order to drive off the latter we are compelled to raise the temperature to about 300 above the boiling point of the former exclusive of the excess of heat required for the primary decomposition described under No 1
- 3rd - When any kind of closed retort or oven is used which is charged internally and the coal receives its heat from the outside it is not merely necessary to raise the temperature of the sides of such retort to the decomposing and distillation heat but to something above this heat as no body can give off any heat by radiation or convection to another body unless it be hotter than the body which is to receive the beat As the quantity of heat communicated by radiation to a given surface varies inversely with the square of the distance from it this difference of temperature requires to be increased very considerably as we enlarge the retort in any manner that increases the distance of portions of the coal from its heated surface
- 4th - The commercial necessity of rapid working in order to economise original outlay upon plant drives us to enlarged retorts acting disadvantageous under No. 3 and to exaggerate the excess of temperature of the retort surface in order to effect rapid communication of heat It will be at once understood that the combined action of these four necessities is to expose the vapour that is formed to the action of the greatly superheated retort walls and thereby decompose it. The primary object of all improvements beyond those directed to economising labour and plant is to overcome or diminish these sources of loss and deterioration and in describing the different forms of retort we shall refer to their intent accordingly.
It will be readily seen that the first of these difficulties is insuperable that the others for themost part can only be partially overcome and thus that the process is necessarily wasteful to some extent All crude oil works present a painful manifestation of this in the flaring jets of gas that illuminated so vividly the surrounding country
These works being for the most part situated in rural districts no use is made of the gas for illuminating purposes and as a source of heat it does not in ordinary cases pay for the cost of conveying it under the retorts inasmuch as the waste coke at hand for fuel The project to supply Chester with the waste gas from the Flintshire Oil Works has been defeated by parliamentary interference in behalf of vested interests
Many oil makers still hope that ultimately the production of this waste gas may be altogether avoided A consideration of the above will probably lead the reader to share the scepticism which the writer has long maintained on this point.
The first step made beyond using the common gas retort was to increase greatly the width and diminish the height of the D retort and forming thereby the flat D now very extensively used and by most manufacturers still regarded as practically the most useful form of retort. As almost every firm has its particular pattern we can only state dimensions generally from 8 to 10 feet is the usual length width from 30 inches to 5 feet 6 inches commonly 3 to 4 feet and height from 12 to 24 inches The verdict of experience runs in favour of further flattening down to the 12 inches.
Fig 1450a represents the general arrangement of Mr. Birkbeck's flat D's in plan and section where ab is the body of the retort c the outlet pipe de the flat condenser fg transverse section of body of retort at f1g1 the retort door and screw clamp i i i furnace and flue. These retorts are 5 feet 6 inches wide. They are in operation at Mr. G.A. Birkbeck's oil works near Padeswood, Flintshire. The advantage of such retorts over the D gas retort is obvious upon consideration of difficulty No .3 The coal is spread over a large surface in a thinner layer and yet a large quantity is included in one charge. All experience goes in favour of spreading out the coal in thin layers rather than packing it a thick mass. The thinner the layer the smaller will be the difference of temperature between the retort itself and the last heated portion of its contents.
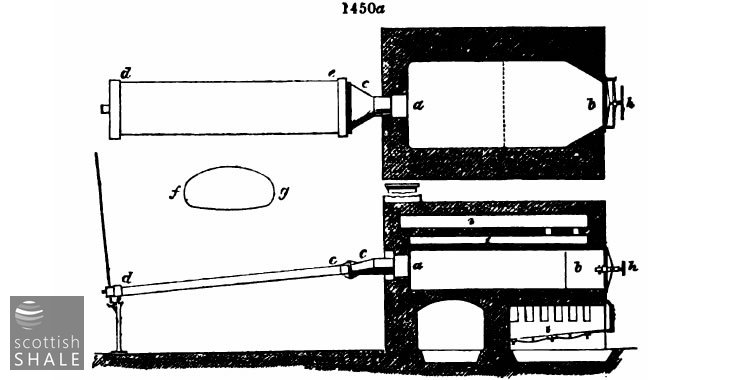
Fig. 1450b represents another form of flat D.; ab, body of the retort, cd, main condensor end outlets; eee, zigzag supplementary condenser, made of cast spouting pipe. It is made by Bryan Johnson of Chester.
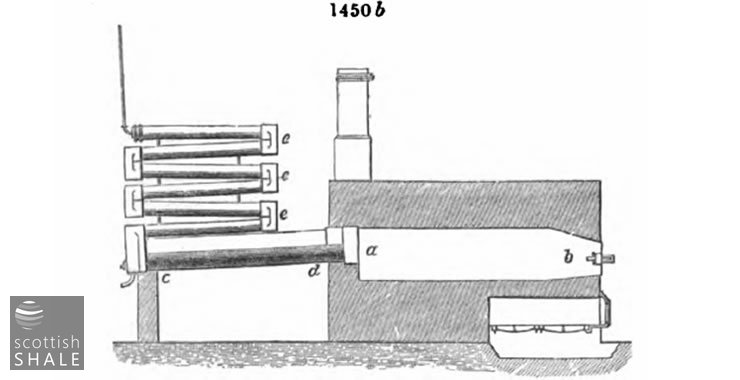
This retort differs but little from the previous one, excepting in having a large outlet with more direct communication with the condenser, and the modified form of the condenser itself. A large outlet is always advantageous, as by its means the vapours more readily escape from the decomposing action of the heated retort and its contents
In order to get rid of these vapours in the most rapid manner possible, Mr.. W. Mattieu Williams, of Ponty Bodkin Works, Flintshire, applies the heat to the top of the retort, which is charged by placing the coal in trays with a bottom of perforated iron. The vapours, which are of high specific gravity, thus escape into a preliminary condensing chamber formed by the lower part of the retort. The objection to this arrangement is the necessity of a larger proportion of fuel, as the charge is only heated on one side.
These retorts have been further modified, in order to obtain a perfect coke from the Flintshire smooth cannel, which when distilled at a high temperature yields nearly a pure carbon. The laboratory process of "fractional distillation" is carried out on a large scale by means of retorts 22 feet long, 3 feet wide, of rectangular section. These are charged with a series of trays 6 inches deep. The fire is placed at one end of the long retort with a flue of its full width extending along the top and terminating in a chimney at the other end; thus one end is much hotter than the other. The retort is open at both ends, and the trays are inserted successively at the cooler end, and pass on to the hottest end, one tray being withdrawn, and the remaining trays pushed forward and another inserted every two hours; the doors being rapidly opened and closed by a simple mechanism. The distillation is thus conducted in a series of two-hour stages. In the first water is driven off, next, some water and the lightest oil ; then a heavier oil ; and finally solid paraffine and pitchy matter, at a gas-making heat, leaving a flameless coke of nearly pure carbon.
This method of working is more costly in labour than that of the common retorts - a difference the inventor hoped to cover by the value of the coke or mineral charcoal, as he terms it. Hitherto, however, the expected applications of this coke to metallurgical operations have not been carried out, which is much to be regretted, as millions of tons of nearly pure carbon might thus be made available from the Flintshire and other cannels.
Another device for affording free escape of the oil vapours from the heated surface of the retort is that of placing a shelf along the middle or upper part of the ordinary D retort. The charge is thrown upon this, and falling over on each side leaves an open space below the shelf, care being taken to spread the layer at the bottom, so as not in any part to reach the shelf. A portion of the vapours travels along this space to the outlet, and thus escapes all contact with the sides of the retort. There are many modifications of the shelf retort in use. Griffith's retorts are cylindrical, the shelf is substituted by a grating of nearly semicircular section, and there are two charging doors, one above and one below the grating. These shelf retorts act very well when the above conditions of charging are fulfilled; but, as very rude labourers are employed for such work, this is seldom the case, and the work being done in the dark through a small door, strict supervision is very difficult to carry out practically.
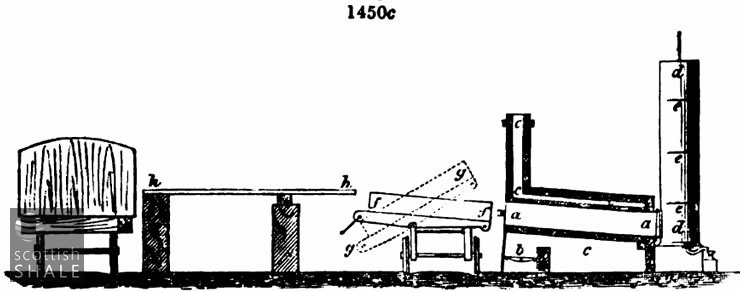
This difficulty is overcome in W. M. Williams' smaller retorts, shown in fig. 1450c, where a a is the body of the retort, a, the furnace, ccc the flue and chimney, d d the condenser, with three beaters or diaphragms eee. f f is a charging tray upon a wagon running upon rails along the front of the bench of retorts, h h,is a strong wood platform which receives the coal from the railway trucks, and from which it is thrown down into the trays, gg shows the position of the tray when tilted for discharging, the end next to the platform being open and the bottom of the wagon moving on a pivot.
The tray f f is divided into an upper and lower compartment by means of hinged flaps, which in the first place are folded back, when about 8 inches depth of cannel is thrown upon the bottom. This part of the charge is spread out in such a manner that its thickness shall vary with the temperature of the different parts of the retort. Then the flaps are folded down, forming an upper shelf. The remainder of the charge is thrown upon this, and the tray thus charged with two layers, and a regulated space between them is pushed into the retort. It is withdrawn by means of a winch and chain attached to the wagon, and tipped, as shown at gg.
The regulation of the layers of the charge to the varying temperature of the retort is effected by a very simple device. The tray itself is in the first place converted into a practical pyrometer by scrubbing the sides with sand till moderately bright, then leaving it for a short time in a fairly heated retort. The tray becomes oxidised with films showing the well-known gradations of straw colour, nut-brown, purple, blue, &c, and by taking the line of one of these colours a curve of equal temperature is marked on the side of the tray. Corresponding with this a strap of strong angle iron is riveted along the insides of the tray, which forms a ledge as well as a strengthening edge bar to the tray. This ledge fixes the height of the bottom layer of coal, which is streaked down to its proper level by means of a heavy rake of the whole width of the tray, and which therefore rests upon this ledge at each end when drawn backwards and forwards over the coal.
These retorts are found to work the cannel slack most advantageously, a thick layer of slack being altogether unmanageable, as it cakes together and resists the passage of the heat to the interior of the mass. The beaters or diaphragms eee are circular plates of sheet iron fixed inside the condenser, and concentric with it. Their diameter is two or three inches less than that of the interior of the cylindrical condenser, and thus there is a space of about an inch all round them. The heated vapours are thereby dashed outwards against the cooling sides of the condenser, instead of ascending as a heated current through the middle and escaping uncondensed by the gas-pipe above. This simple device has overcome the practical objection to upright condensers of large diameter and moderate height, and since their introduction in connection with these retorts they have been adapted to many other forms of retort, and in Flintshire are now generally preferred to either the horizontal condenser, fig. 1450 a, or the pipe condensers, 1450 A. They are cheap and compact, and not liable to derangement from clogging. Very complex forms of condensers were used in the first stages of coal oil-making, worm tubes, with water tanks and hydraulic mains of various patterns. It is now found that simple radiation is a sufficient cooling agent
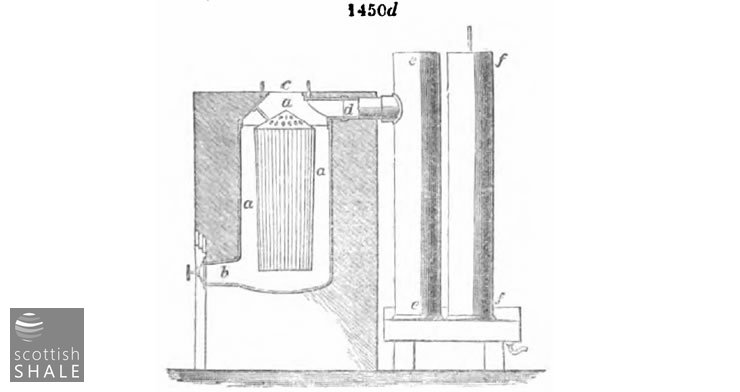
Fig. 1450d represents in section the upright retort of Mr. Holmes of Ruabon, where a a a is the body of the retort, b the discharging outlet for the coke, c the charging mouth, d the vapour outlet, ee and ff the condensers. In this retort the internal cage shown in the figure serves the purpose of the shelves, &c. already described, as by its means the charge forms a layer occupying the space a a a in contact with the retort walls, while the vapours pass into the cage and thence to the condenser. It is easily charged where the coal is brought from an upper level.
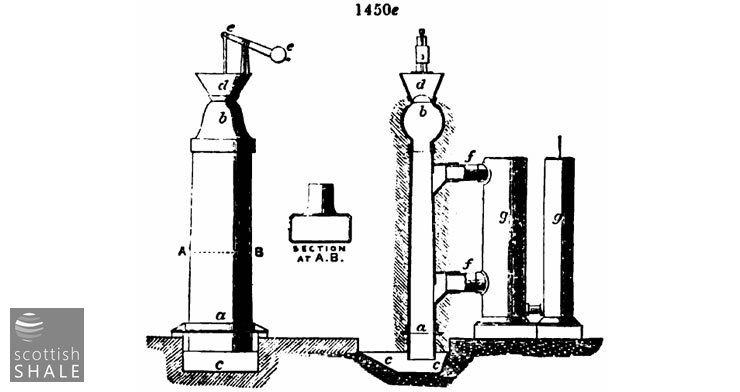
Fig. 1450e represents Bryan Johnson's modification of the Scotch upright retorts, which work a continuously descending charge. Supposing the retort to be filled, the valve at a is opened, and a portion of the coke let down into the receiving water tank, c c. The hopper d being filled with a corresponding quantity of fresh cannel or shale, the valve b is raised by means of the lever e e, and the retort is filled. This is repeated at short intervals, and thus the charge is gradually worked downwards. Theoretically, these retorts should be hottest at the bottom, and the heat gradually diminish upwards, but practically there is great difficulty in arranging the flues to obtain a regular gradation of heat on account of the rapidity with which the heated gases of the flues ascend when the draught is at all free.
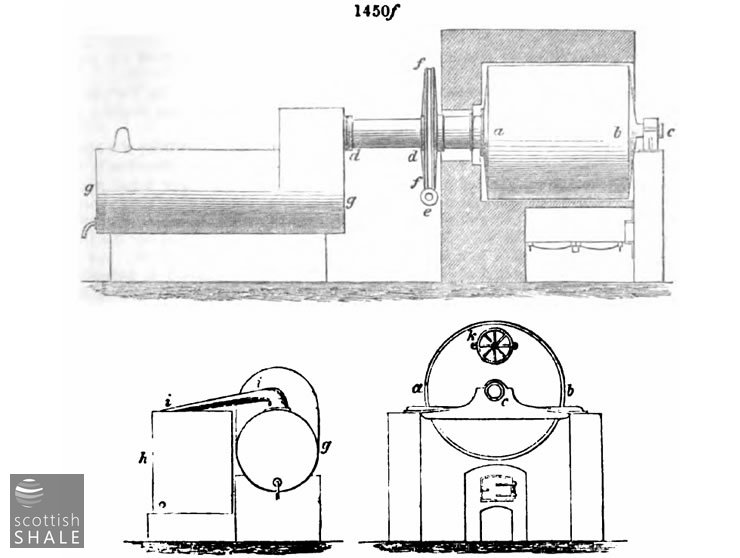
The revolving retort is an American invention. It is shown in elevation and section in fig. 1450f, the lettering being the same in the sections and the elevation. a a is the body of the retort, a cast-iron cylinder (wrought-iron have also been used) usually about 7 feet diameter, and 7 feet long. The cylinder turns on the axles c and d d, the latter, d d, is hollow and serves also as the vapour outlet to the condenser g, which has a second or supplementary condenser shown in section at a, connected with the first by the swan neck i i. The cylinder or body of the retort is turned very slowly by means of an endless screw, e, working in a toothed wheel, f . The charging door, k, is on the opposite face of the cylinder. The heat is communicated from the furnace by means of arched flue which embraces the whole of the cylinder. To charge the retort the door,k, is turned upwards as shown in the figure; to discharge it is by a half revolution from this position brought to the lower side.
The action of these retorts will be easily understood. The charge is continually rolled over, and thus fresh portions are brought in direct contact with the heated surface. By this means a very rapid distillation is effected. In this respect they are most efficient. The objections to them are their costliness in the first place, and their liability to crack, from the unequal expansion of so large a surface of metal. They cannot be protected all round, as ordinary retorts are, by a casing of fire bricks, and being thus exposed to the direct action of the fire are rapidly destroyed, especially if great care is not taken to remove the lining of carbon deposit which forms on the inside. When ordinary cannel is used, they have to be cleaned out weekly, which involves a serious loss of time in cooling down and reheating all the surrounding brickwork. This difficulty is to a great extent overcome by working lumps of hard shale with the cannel, which is especially necessary when cannel slack, for which these retorts are best adapted, is used. Where the material to be used is liable to soften and become at all adhesive when treated, these retorts are utterly useless. When it forms a hard clinker coke, they may with careful management be advantageously used, as the quantity of work done by them is very great.
Another difficulty is presented by a very friable material which readily crumbles into dust, as such dust flies over with the vapour and makes a very dirty oil.
Among the earlier efforts to improve the process of distillation of coal, &c., was a the application of superheated steam. Several patents hate been secured for this, the general object being to drive the heated vapour through a mass of coal broken into small pieces, and thereby apply the heat directly to each fragment, thus completely avoiding the third source of excessive temperature, besides affording an effectual means of regulating the temperature while diffusing it equally throughout the whole mass.
This method, though so admirable in theory, has failed in practice, after being well tried by Messrs.. Young, by Messrs.. Lavender and Co. at the Canneline Oil Works, Flintshire, and by others. It is now, as far as we are aware, altogether abandoned. The difficulties that have led to its abandonment were mainly the costliness of the superheating process, and the great amount of steam required to be formed in the first place, and then to be condensed. It must be remembered that while the latent heat of steam is equal to about 1000° Fahr., that of the hydrocarbons primarily to be distilled is not above one-tenth of this; thus every pound of steam requires for its condensation about ten times the amount of cooling surface, which is necessary for the condensation of a pound of oil vapour ; and the complete condensation of the steam is necessary, as it obstinately retains an important quantity of oil vapour diffused through it .
The use of heated gases, such as nitrogen, carbonic acid, &c, in the place of steam, overcomes this difficulty, but the cost of preparing the gases renders their application equally impracticable on the primary score of economy.
The meerschaum retort is a modification of the principle of distilling the coal by internal application of heat. This is effected by means of a large chamber or kiln, rather than retort, constructed of fire-brick and shaped like a huge tobacco pipe- bowl, with which an exhaust-pipe like the stem of a tobacco-pipe communicates with the bottom. This exhaust-pipe communicates with suitable condensing chambers. The bowl or kiln is charged with the cannel or shale, on the top of which is laid a stratum of burning coke or a mixture of coke and slack. As soon as this upper stratum is in a state of full combustion, the exhaustion is commenced by means of a steam jet, and the heated products of combustion are drawn down through the charge. That portion immediately below the fire is of course the first acted upon, the action commencing with a distillation of the most volatile products. As the heat increases, the more stubborn and denser vapours are driven downwards through the lower mass, and by their heat commence the distillation there. Subsequently, the upper layer of cannel having all its volatile constituents driven off, becomes a coke, and at this stage is so highly heated as to burn and give off combustion products, viz. carbonic oxide, &c., instead of distillation products, thus serving as fuel for the cannel below, and so on till the mass is coked to the bottom. When this is completed, the steam jet is turned off, the exhaustion ceases, and the charge is drawn from below, a portion of it being used in its burning state for starting a neighbouring kiln, which should always be charged ready to commence working when its predecessor has reached this stage.
The meerschaum is an American invention, was first tried on Long Island with Boghead imported from Scotland, but shortly afterwards abandoned. Its projectors maintain that the abandonment was purely the result of the competition of petroleum springs, and not due to any defect in the principle of the meerschaum itself.
Mr. Holmes is now erecting some of these retorts in the neighbourhood of Ruabon, and is very sanguine of their success. The first trials already made have not been quite satisfactory, the condensing arrangements being insufficient, and an extension of these is now in course of construction. The size of Mr. Holmes' meerschaums is 12 feet high, and 8 feet diameter internal measurement. They are to be charged to a depth of 10 feet, and to contain 12 tons of cannel.
The refining of the liquid portion of the crude oils is still conducted in the manner already described as Messrs.. Young's method. A great many patents have been secured, a large proportion of them evidently based upon the theory that the refining of these oils is simply a process of oxidation analogous to that of the bleaching of vegetable colours. Some degree of oxidation undoubtedly does take place in the course of the refining process, but this is far from being the whole action. The sulphuric acid appears to act chiefly as a carbonising agent, and by heterogeneous adhesion to the carbonaceous or pitchy colouring matters which it carries down with it in the form of "acid tar." The theory of the action is, however, by no means fully understood. It still offers a most interesting field for a thorough investigation.
Among the many processes patented may be named the use of hypochlorite of lime, the application of chlorine gas to the vapours of the oils, of nascent chlorine to the liquid oil by the decomposition of hydrochloric acid or chloride of sodium with black oxide of manganese, the use of bichromate of potass and other chromates, and of free chromic acid, of the permanganates, and almost every known oxidising agent.
The sulphuric acid treatment is the only method which has been found commercially successful. The proportion of acid required depends upon the oil, and must be determined by experiment. Generally speaking, the heavier oils require more acid than the lighter; but even this rule is subject to special exceptions.
Many forms of agitators have been adopted, from simple tubs with a paddle to very complex devices worked by steam power; the problem, however, is merely to keep a heavy liquid, sulphuric acid, stirred up amidst a lighter one, the crude or "once run" oil. A cast-iron vessel fitted with paddles, working on an axle similar to a common churn, is the apparatus generally used. Upright cylindrical vessels, with an Archimedean screw working vertically to raise the acid from the bottom, have been used, but not extensively.
In some refineries the crude oil is treated with the acid and alkali, but more commonly it is "once run" as already described. In all the stages of distillation for the refinery, the use of superheated or dry steam is found very advantageous, not as the primary source of heat, but as an auxiliary. In accordance with the well-established law of diffusion of gases, the vapour from the boiling oil will diffuse much more readily into an atmosphere of steam than into one of its own vapour, and thus the superheated, or simply the dry steam, enables the distillation to be conducted at a lower temperature than -would be necessary without it, which is a matter of considerable importance, not merely as regards the quantity of work done with given fuel, but also as affecting the quality of the oil produced.
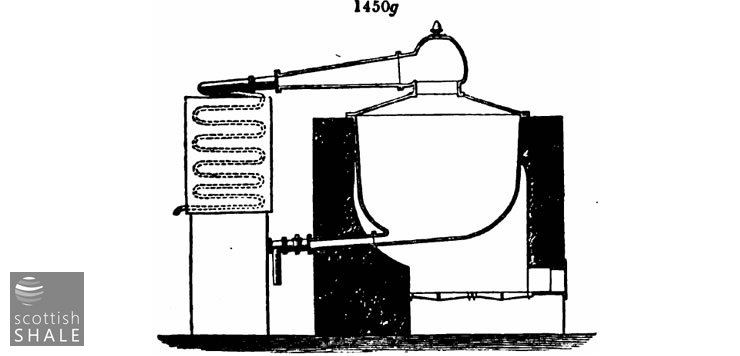
The form of still most commonly used is shown in fig. 1450g, usually of a capacity of 1,000 to 2,000 gallons. Much difference of opinion prevails among refiners as regards the merits of cast or wrought iron. Many serious conflagrations have lately occurred from the sudden cracking of cast-iron stills, which have led to a much more extensive use of wrought-iron than formerly.
It is a common practice in the first running of crude oil to use a wrought-iron still, or still of cast-iron with bottom outlet pipe, like that in fig. 1450g, for the first part of the process, until the heavier products begin to run over, then to run out the residue from this still into a small round bottom still, without bottom outlet, and then " coke down," that is, carry on the distillation to dryness. By this means the most dangerous stage is carried on in the smaller still, which is far less liable to rupture. Wrought-iron stills cannot well be used for coking down, the great heat required destroying the rivets.
In the refining of the solid paraffine considerable progress has been made, the method now most commonly adopted being totally different from the sulphuric acid treatment above described as Young's process.
In the first place, the crude oil is distilled over to dryness, "coked down", as already described. The heavy oil obtained from the latter stages of distillation is found to contain large quantities of bright crystalline scales of solid paraffine in suspension. It is a curious fact, that although this solid paraffine exists in the crude oil, it does not crystallise out in this manner until subject to a second distillation. In the crude oil, the pitchy constituents seem to cling to the paraffine particles and hold them back from crystallisation, bo that they form an amorphous greasy mass when the light oil only is distilled off from the crude. This grease, however, when distilled gives over a rich lubricating oil of pale brown colour, with the paraffine crystals in such a state of free suspension that they are readily separated at a low temperature. This separation of " brown paraffine scale" is effected by " bagging " and pressing. The bagging is simply a filtration in canvas bags, which are usually filled and tied up, then heaped together or thrown into perforated boxes till the greater portion of the oil filters out. The contents of the bags are then submitted to a gradually increasing hydraulic pressure till the utmost possible degree of dryness is obtained in the cake of crystalline scales.
The quantity of solid paraffine thus obtained depends in a great measure upon the temperature at which these operations are conducted, as the oil is a solvent to the paraffine, and the quantity it is capable of dissolving rapidly increases as the temperature rises. In small works this separation of paraffine is only conducted in cool weather. In larger works refrigerating machines are used. The purification of the brown paraffine scale thus obtained is now effected by the simple process of dissolving it in a hot solution of the mo6t volatile "paraffine spirit" obtainable. American petroleum spirit is the best adapted for this purpose, it is cheap and more volatile than coal oil spirit.
The scale having been dissolved in about an equal weight of spirit, the solution is set to cool in suitable vessels. As it cools, the solid paraffine recrystallises, in the course of which action it rejects the impurities associated with it, giving up its brown colour and the liquid solvent. The cooled mixture of crystal and spirit is again submitted to pressure, whereby the spirit is separated, and the crystals, now of a cream colour, are again dissolved in colourless spirit and the same treatment repeated. A third treatment is usually necessary to obtain perfect purification, when beautiful crystals of exquisite snowy whiteness are obtained, presenting the most perfect contrast imaginable to the coal from which they are derived.
The chief drawback to this process is the waste of spirit by evaporation during the cooling and pressing processes. By careful and intelligent management this waste may be materially reduced. The refuse spirit, which has received the colouring matter and other impurities from the brown scale, is easily refined by simple distillation, and may be used again and again. The brown refuse left in the still may be treated afresh as crude paraffine scale, as there always remains a portion of paraffine in it which continued in solution when the rest crystallised out. This, however, is of inferior quality, having a lower melting point, and is usually sold in a semi-refined state for making common candles, burning in miners' lamps, &c, &c.
This mode of refining paraffine is not only cheaper than the acid treatment, but when skillfully conducted produces a superior article with a higher melting point than the paraffine which has been subject to the acid treatment and redistillation. Whiteness, freedom from smell, and a high melting point, are the commercial tests upon which the value of paraffine depends.
The importance of the latter may easily be understood when we consider that the melting point of the best paraffine is but 125° F., while inferior qualities are much lower. Paraffine, like wax, resin, and such substances, softens at many degrees below its melting point ; hence candles made of an inferior paraffine are liable to bend over into strange shapes in a heated ball-room, or in a hot climate. This was very vexatiously and absurdly exemplified at the coronation of the Emperor Maximilian in Mexico, when at one of the festivals all the beautiful "spermaceti" candles, ordered expressly from England, and numbering several thousands, though brilliantly successful at first, gradually softened as the throng increased, and finally bowed over altogether, flaring hideously and guttering in streams upon the dresses of the visitors.
In order to remove the last traces of the spirit, which if left behind lowers the fusing point, besides giving its odour to the paraffine, the scales are fused and heated to about 240° F., care being taken to go no higher than this, as at 260° the paraffine acquires a yellow colour similar to that of bees'-wax. It is, therefore, necessary that the spirit should be freely and fully volatile at or below 240°, and that all the heavy oil should be separated in the earlier stages of the process. This fused paraffine is run into molds and sold in cakes as " paraffine wax," which is now becoming the great staple material for the manufacture of the better class of candles. Every year the price of these candles has come down lower and lower, in consequence of the increased production by improved methods The recent improvement will doubtless bring this beautiful material within the reach of all classes, by reducing it to a price but little, if at all, exceeding that of common tallow. W.M.W